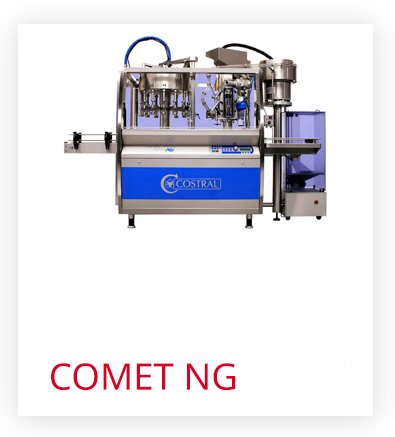
COMET NG
The COMET bottling unit production rate can vary from 1,000 to 3,200 bottles/hour (0.75 liters) depending on the model selected.
Bottle selection at inlet is done using an Archimedes’ screw. The bottles are routed to the filler chute by 8, 11, 14 or 16 nozzles, height adjustable using an electric control panel (180 to 380mm).
How is bottle filling optimised using the COMET NG group?
It offers a simple gravity filling principle, with no suction, no contact with ambient air, no overfilling and using assisted gravity with gentle vacuum (depending on the liquid recommendation).
A top feed either fills by gravity or using an external pump connected directly to the unit.
A pneumatically operated solenoid valve is built into the liquid inlet (requiring access to compressed air). The head space level in the bottle can be adjusted with millimetric accuracy using the electric control panel.
Bottles are then transported by conveyor to the “revolver” capping column which can handle several different capping methods (including corks, crown caps and screw caps) using one single rotation. It offers electric height adjustment (180 to 380mm).
The corking cycles are managed electronically ensuring corks are tightened slowly followed by rapid insertion to secure them. The corking head includes a stainless-steel compressor with four corking jaws that can be easily detached (filling system). A high-performance vacuum pump draws air from the neck of the bottle, prior to the cork being secured. The cork hopper fitted with a dust collector is positioned on the top of the column.
The electronic speed control allows the production rate to be accurately set (from 0 to 3,200 bottles/hour depending on the model)

GALAXY
The GALAXY Monobloc enables multiple injections, of water, sterilizing solution, neutral gas or filtered air, using fixed and mobile injection drawers (entry cannulas).
How powerful is this rinser? The optimal use of space reduces the footprint of the machine offering an unmatched use cycle time (bottle turn around = rinsing + draining). The injections are particularly effective and bottle draining time is extremely long.
Example of total use cycle time (bottle turn around) at a rate of 2,000 bottles/hour: 32 seconds.
The tank can be filled by simple gravity or by an external pump connected directly to the unit.
The filling process operates on a simple gravity principal (no suction, no contact with ambient air, no overfilling) or by assisted gravity with gentle vacuum which enables vacuum filling avoiding ambient air entering into the tank.
The unique feature of this filler is that it comes from an external control for nozzles. The nozzle opening control is a star with three positions (filling, levelling and standby).
Filling is carried out with great accuracy, using a level regulator handled via a control panel. The liquid level in the filling tank is managed by a stainless-steel float with an “empty tank” safety mechanism. A pneumatically operated solenoid valve is built into the wine (or other liquid) inlet enabling flow management in real time. In order to achieve millimetric accuracy, the head space level in the bottle can be set using the electric control panel.
By filling from above, the process ensures that all the liquid is used, « right up to the last drop ».
Featuring a 316L electropolished, stainless-steel unit, the GALAXY Monobloc filling system is suitable for both hot and cold liquid filling such as wines, fruit juice, alcohols, vinegar and water.
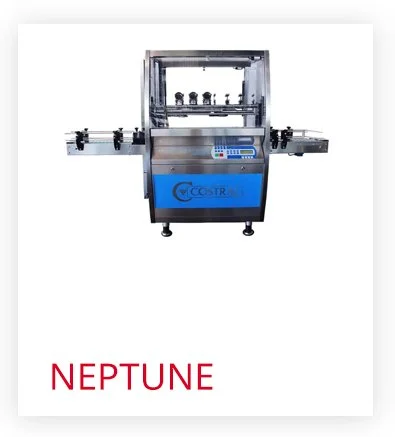
NEPTUNE
Designed in stainless steel, the NEPTUNE rinser provides the most efficient sterilizing, cleaning and maintenance.
Three by three or four by four bottle selection at the inlet, using an Archimedes’ screw. Bottles are transported, gripped in a clamp to be re-positioned and placed into centering cups. The start up cycle begins with a timed rinse using a fixed injection drawer. Then bottle magazines are sent backwards prior to turning, ensuring a long draining time.
As a result, the total use cycle time (bottle turn around) may vary by up to 40 seconds (depending on run rates). This is the advantage of our NEPTUNE rinser: Optimal use of space available offering an unmatched use cycle time.
At the outlet, bottles are grabbed by the clamp, then turned over and placed on the moving conveyor system to feed them through to the filler.
To adapt to your production volumes, an electronic speed control makes it possible to accurately set your production rate (from 0 to 4,000 bottles/hour).
To manage the machine’s operation, a control panel with a flexible keyboard is placed on the front of the rinser with a digital screen displaying:
-the model of the bottles being processed,
-adjustment settings,
-production incidents occurring.

HYDRA
The HYDRA washer dryer provides optimal cleaning and drying for your bottles using functionality designed to enhance your productivity.
The bottles are fed by conveyor and detected by a sensor at the machine entry in order to pass on to the washing area which operates using three rotating brushes. In addition, brushes for the base and the cap are used (two fixed base brushes + one cap brush).
The bottles are routed to the drying area where two hot air blast nozzles are used, produced by a turbine mounted in the machine frame. This process ensures that bottles are completely dry.
Our washer dryer can be perfect synchronized with your other bottling/labelling machines, thanks to two electronic speed controls (conveyors and selection star for bottles). You’ll increase your productivity, handling bottling and/or labelling processes at a run rate to best suit your production requirements.
HYDRA offers you a secure bottle cleaning solution. At the outlet, an anti-jamming mechanism is in place to ensure the machine cuts out if the labeler stops.
We also offer precision monitoring via a control panel which tracks bottles throughout the production process. A 4-line digital screen displays the bottle counter, the run rate and the pitch of the bottles in the drying area as well as signaling any issues during production.
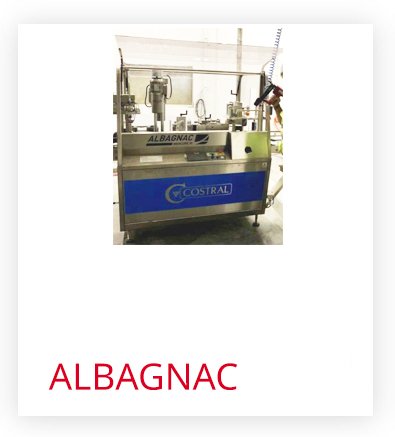
ALBAGNAC
ALBAGNAC machines offer adhesive, rotary or linear labelling solutions, from 0 to 6,000 bottles / hour. A range on which we have become experts, thanks to our 30 years of partnership.
Whatever your business, our adhesive labelers adapt perfectly to all types of containers, shapes and caps. ALBAGNAC labelers provide both capping and/or labelling for filled bottles, as well as jars or other containers you may need.
Prior to labelling, ALBAGNAC machines are able to cap bottles.
They have an automated capping dispenser with a long-range loading magazine (inclined plane), neck centering clamp and ejector-insertion driver.
The capping station has a slow descent and fast ascent (short low neutral position) and a crimping head with eight rollers (mounted on ball bearings) of TS 8 for standard aluminium, tin or complex metal caps.
The bottles are then transported to the labelling unit, where they are secured by a pneumatically operated door that rotates during the labelling process. In order to provide perfect finishes, the machines have a star sensor to detect the bases by notching the bottles. This system can position labels centrally in line with glass engraving.
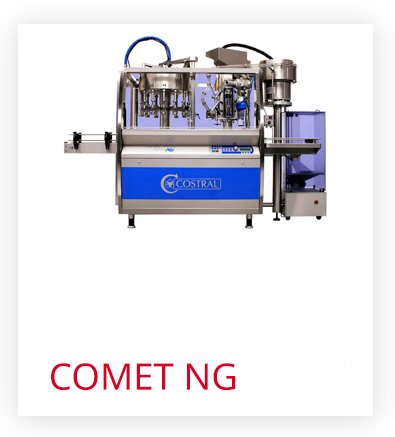

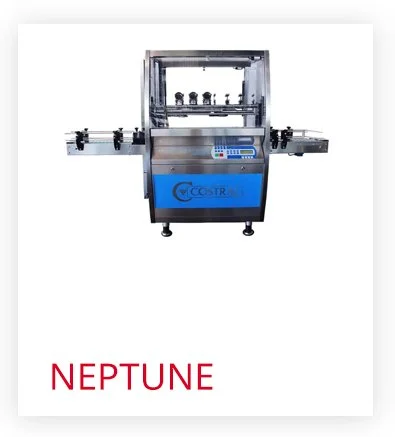

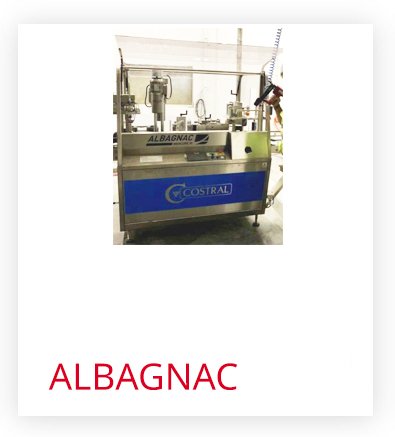